Module Assembling and Evaluation
Solar cell modules are required to possess long-term quality assurances that they will work properly in an array of environmental conditions, including temperature differences of dozens of degrees, high humidity, strong winds, a dusty environment, strong UV rays, and sunlight, for 10 to 20 years. Therefore, the modules must be highly reliable and endurable. Usually, quality assurance of a solar battery is not required for its cell unit only, but for the entire module, which includes PV cells. Therefore, module material testing should be conducted using the same methods as those of the module.
No. | Analysis / Evaluation | Instruments |
---|---|---|
1. | Evaluation of electrode joints (After acceleration test) | Non destructive inspection instrument |
Tensile test of electrode joints | Material testing machines | |
2. | Rheological evaluation of sealing films (EVA) | Rheometers |
Thermal curing of sealing films (EVA) | Thermal analyzers | |
Deterioration test of sealing films (EVA) Analyzes chemical changes in deterioration processes by light, heat, and oxidation, and evaluates weatherproofing capabilities. |
(UV/Py)GCMS | |
3. | Cover glass, Transmittance evaluation of sealing films (EVA) The cover glass has two roles - 1) passes light as much as possible and 2) After light is reflected by a cell, a cover glass (an anti-reflectionfilm) reflects the light back into the cell. |
UV |
4. | Peeling and tensile test of EVA film sealant and weatherproof films (back sheet) | Material testing machines Fatigue testing machines |
Load test of module | ||
Bending test of module |
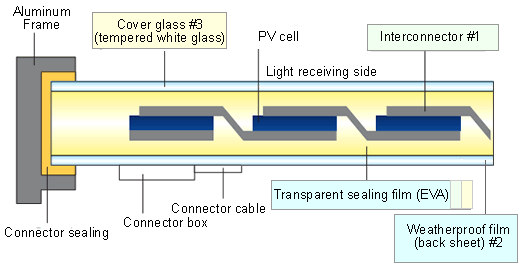
#4: Tensile test, bending test, and load test of the connector are required by IEC 61215 and IEC 61646. Regarding tensile testing of the connector, Shimadzu offers two types of testing methods: tensile testing of connectors on parts and torque testing of connectors on parts. In addition, peeling testing of cover glass from a module is important. |