Analysis of the Failures of Surface-Hardened Gears
—Analysis of Failure Starting Point by Hardness Distribution Evaluation and Carbon Content Mapping—
The wear resistance and durability of load-bearing automotive mechanical parts, such as shafts, bearings, and gears, are improved by increasing their hardness by induction hardening, nitriding, carbonation, coating technologies, etc. Normally, the quality is checked by measuring the depth of the hardened layer; however, there is an increasing need to evaluate the hardness distribution because the hardness may be uneven depending on the shape of the part and processing conditions. Likewise, with welding and pressure welding, a more detailed evaluation can be performed by evaluating the hardness distribution. Also, in a normal hardness test, a section is cut out and the test is performed on that section, but there is a need to test the hardness of the part using the shape as it is. Hardness mapping is sometimes analyzed in detail together with composition mapping of the carbon content. Introduced here are the latest topics in hardness testing and composition mapping to deal with these needs.
Evaluation of Unevenness in Hardness of Automotive Parts
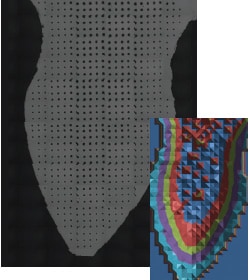
Mapping the Hardness of Gears
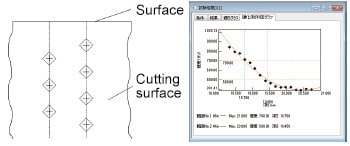
Evaluation of the Depth of the Hardened Layer (JIS G 0559, ISO 3754)
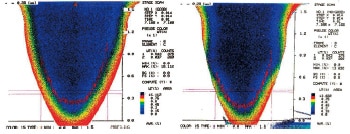
Mapping the Carbon Content of Gears

HMV-G31-FA Series
Fully automatic tester that can measure hardened surface depth and perform hardness mapping
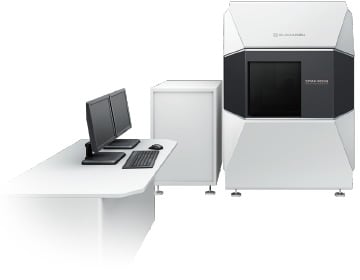
EPMA Series
Capable of evaluating composition distributions, such as carbon content mapping.
- The test positions can be easily specified after automatic recognition of the sample shape using the edge-detection function, so not only can the hardened layer depth be evaluated, but hardness mapping can also be evaluated easily.
- The functional design allows for ample working space in the depth direction. In addition, the space in the center of the frame is large, so a greater number of parts can be tested as they are.
- The high X-ray take-off angle of the Shimadzu EPMA allows it to obtain clearer distributions on uneven or curved samples, so the system can be used for various applications and materials.