Cellulose nanofibers
Given that cellulose nanofibers(CNFs)offer attractive physical characteristics, such as light weight, strength, and hardness, they not only enable materials with advanced functionality, but are expected to be used as a reinforcing material that can reduce the weight of composite materials. In contrast to advanced nanomaterials made from petrochemical fuels and inorganic substances, CNFs are made from plant biomass. In addition to being environmentally friendly and safer, they have been confirmed to offer superior performance.
Mixing CNFs into the pulp used to make speaker diaphragms, for example, enabled higher quality sound reproduction by improving the Young’s modulus of the diaphragm and broadening the range of high-frequency sounds they can produce. Adding CNFs to the midsole of running shoes achieved a lighter shoe and superior cushioning performance. Thus, CNFs have started being used in many everyday products, such as rip-resistant disposable wipes, ballpoint pen ink, cosmetics that provide a young appearance without feeling sticky, and waterproof cosmetic face masks.
Applications for CNFs are expected to continue expanding; examples include lighter and stronger CNF polymer composite materials used as structural materials in aircraft and transparent CNF panels enhanced with functionality for conductivity.
Morphological Observation of Cellulose Nanofiber
Because CNFs are produced by the grinder method, in which cellulose is mechanically defibrated, optimization of the defibration conditions is required for efficient production of larger quantities of CNFs. Therefore, morphological observation was performed focusing on the fibers in the defibration process, which had not been considered important in the past. This article introduces an example of morphological observation of fibers during the mechanical defibration process using a scanning probe microscope (SPM) and laser scanning microscope (LSM).
Samples were prepared by defibrating a broadleaf tree pulp sheet by the grinder method, followed by dispersion in water. Due to the large size of the untreated fibers and fibers after one treatment, these fibers were observed by LSM. Fibers after two to five treatments were observed by SPM, and the average fiber diameters were calculated. Fig. 1 shows the observation results. Although the untreated fibers are in a bundled condition, it can be seen that the fibers unravel and become progressively finer as defibration treatment proceeds.
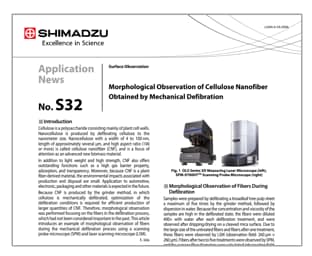
Also, the fibers obtained by performing defibration treatment five times (Fig. 1, lower right) were observed with high resolution by SPM (observation field: 250 nm × 250 nm).
Please download the application news to see the result.
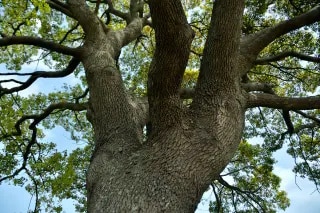
The water dispersibility of CNFs depends on the fiber diameter and shape. Moreover, As the functional groups modified on the surface of cellulose nanofibers provide various properties, such as transparency and water dispersibility, it can be expected to be applicable to automotive components, electronic materials, and packaging materials.