Reducing Weight
Reducing Weight
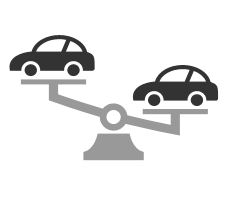
Weight reductions are needed in order to improve fuel consumption. New lightweight, high strength materials are becoming a focus of interest. In terms of metals, these include high tensile steel materials and aluminum alloys, and in terms of resins, these include CFRP and other composite materials.
They are evaluated from the perspective of strength, fatigue characteristics, impact characteristics, workability, composition, and structure.
Multifaceted Evaluation of EV Hollow Shaft
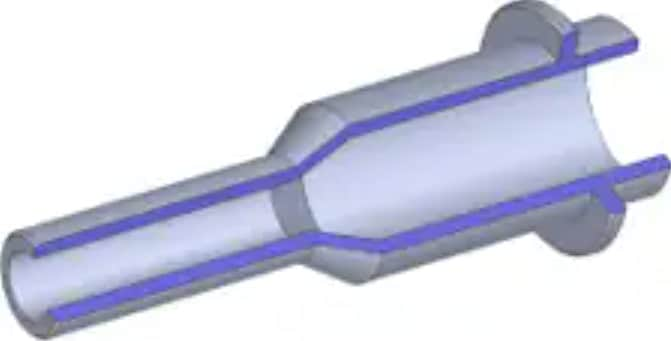
Image of Hollow Shaft
To expand the use of electric vehicles (EVs), reducing the weight of vehicle bodies is necessary to increase the distance that they can travel. Reducing the weight of the shaft is particularly important because, in addition to improving the distance that can be traveled, this weight reduction is expected to improve the responsiveness of the motor by reducing the inertia.
Application news/information
Press workability evaluations
Pressed parts made of lightweight materials with poor workability, such as high tensile steel, aluminum alloys, and magnesium alloys, are essential for reducing the weight of transportation equipment. Repeatedly modifying the die to achieve a target shape not only increases costs, but also lengthens the development period. One solution currently being tried is to reduce the number of actual samples evaluated by using simulation to predict forming problems in advance.
Application news/information
Evaluations of composite materials
Carbon fiber reinforced plastic (CFRP) has a higher specific strength and rigidity than metals, and is used in automotive to improve fuel consumption by reducing weight. However, CFRP only exhibits these superior properties in the direction of its fibers, and is not as strong perpendicular to its fibers or between its laminate layers. When force is applied to a CFRP laminate board, there is a possibility that delamination and matrix cracking will occur parallel to its fibers. Furthermore, CFRP is not particularly ductile, and is known to be susceptible to impacts. When a CFRP laminate board receives an impact load, it can result in internal matrix cracking and delamination that is not apparent on the material surface.