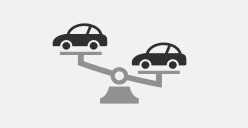
- Press workability evaluations
- Evaluations of composite materials
The technologies used in automobiles are being refined and innovated on an ongoing basis to improve safety, comfort, and to reduce the impact on the environment. Automobile production sites have always competed to build reliable automobile parts quickly and cheaply, but recently there has been a greater emphasis on evaluating the performance of not only individual parts, but also entire modules, which has necessitated more advanced automotive analysis, inspection, and testing. In addition to this, further analysis and evaluation is required for vehicle electrification, battery development and implementation, weight reduction, model-based development, and other strategies to help achieve carbon-neutrality.
Shimadzu supports major automobile OEMs and their global supply chain partners with state-of-the-art instrumentation. We provide various solutions including automotive parts and material evaluation, improvement of LCA (Life Cycle Assessment) and reducing environmental burdens, and integrated analysis to prevent product defects. Our analytical instruments, inspection systems, and testing machines are the perfect fit for extensive evaluation requirements found in automotive development, quality control, and environmental compliance. Learn more about our solutions below.
To help achieve carbon neutrality, governments and companies around the world are pursuing initiatives for weight reduction and CASE (Connected, Autonomous, Shared, Electric) as a framework for next-generation automobiles. This e-book introduces a range of evaluation and analysis technologies that bolster the advancement of lightweight automobiles that exhibit CASE attributes.
Reducing weight
Electrification
Multi-material
Module
Deterioration/Degradation Analysis
Reducing weight
Multi-material
VIAQ
Comfort and quietness
Module
Reducing weight
Electrification
Multi-material
Comfort and quietness
Module
Electrification
Improvement of LCA (Life Cycle Assessment) and reduction of environmental burden solutions for technical issues
Quantitation of sensory tests
Multilateral evaluation is effective for correctly evaluating materials that are used for automotive parts. Shimadzu will assist you with material evaluation with a wide range of analysis and test instruments lineup.
Crystallization
Density
Product Shapes
Strength Fatigue
Surface
Please visit our US website.