Quality Center Opened
in December 2013
Equipped with the equipment and expert staff necessary to ensure safe and user-friendly products can be delivered to customers.
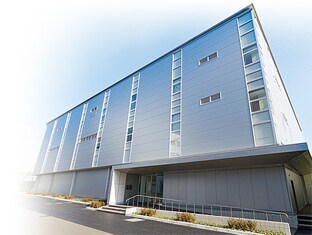
Quality Center
built at Sanjo Works
In December 2013, Quality Center was opened as a central collection of our internal equipment and functionality for ensuring quality at every stage of the product life cycle, from design and development to manufacturing, and for strengthening and improving quality in the marketplace. The approximately 5,500 m2 three-story steel frame building expands our facilities for evaluating quality, such as by testing safety during the development stage, and for improving operability. In addition, it is equipped with equipment and staffed with experts for supporting quality control during the manufacturing stage or for analyzing and resolving any problems that occur in the marketplace.
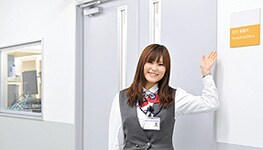
Reception office
Reception responds to inquiries from users of Quality Center
Customer entrance
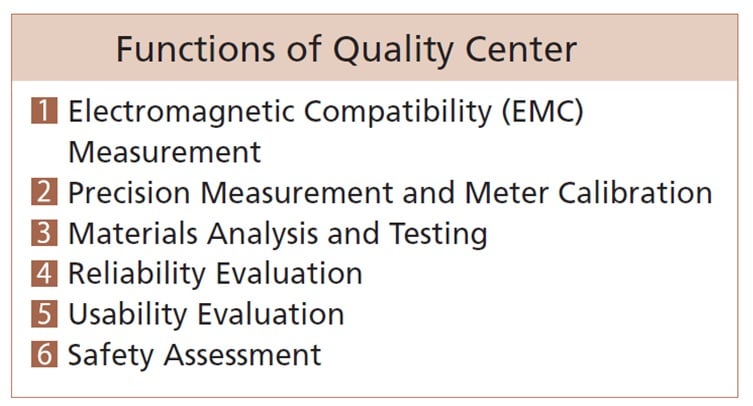
Functions of Quality Center
The following describes how the activities at Quality Center help improve
the quality of Shimadzu products.
Materials Analysis and Testing
(1)Quality Control for Materials
Quality control verifies that the materials used in products are consistent with specifications. For example, ingredients are analyzed to make sure the materials satisfy specified requirements and do not contain any harmful substances that could have a negative effect on the environment or materials are pulled apart in tensile tests to make sure they have appropriate strength. Furthermore, the hardness and structural composition of materials are investigated to verify appropriate treatment processes have been performed.
(2)Materials Analysis for Identifying Causes
If a problem occurs in the marketplace, we can analyze the problem to identify the causes. For example, we could use an electron probe microanalyzer (EPMA), which is a Shimadzu product that is able to analyze the constituent elements of a material at high resolutions, to determine how the product failed or what a contaminant is made of. Various other analytical techniques can also be used to quickly identify and resolve the causes.
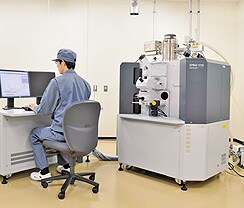
Using an EPMA for analysis
EMC Measurement
Electromagnetic compatibility (EMC) means electromagnetic interference between electrical devices. It involves both reducing any influence that electromagnetic waves generated from electrical devices may have on other devices in the surrounding area and also increasing the ability of electrical devices to resist malfunction caused by exposure to electromagnetic waves from the surrounding environment. For example, it tests whether or not Shimadzu products could be activated by electromagnetic waves, such as from a mobile phone or from a large number of Shimadzu products placed side-by-side. These tests are conducted in a room that is unaffected by external electromagnetic waves, referred to an anechoic chamber. Quality Center has three anechoic chambers of various size, including one compatible with the 10-meter method. This means tests can be performed for compliance with regulations specified in any country or region.
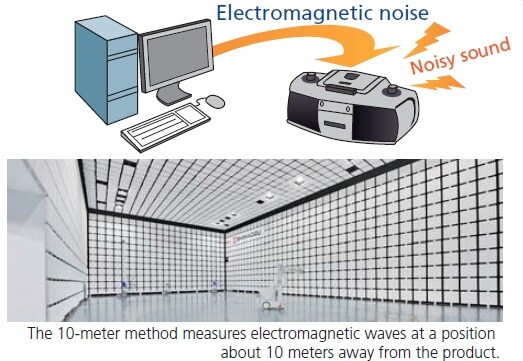
The 10-meter method measures electromagnetic waves at a position
about 10 meters away from the product.
Reliability Evaluation
(1)Temperature and Humidity Testing
Products or parts are subjected to various temperature or humidity loads to confirm their resistance to such loads. For example, conditions are simulated to test whether or not systems malfunction when exposed to temperature or humidity levels that exceed specifications by a given margin.
(2)Vacuum Testing
In a vacuum, even slight amounts of contaminants remaining on parts can negatively affect product performance due to the extremely low number of gas molecules. Therefore, specialized equipment is used for testing.
(3)Endurance Testing
Products include parts that are used on a daily basis, such as covers, doors, cables, and switches. Therefore, these parts are tested using specialized testing instruments that open and close the covers and doors several tens of thousands of cycles to verify that the product will still function properly after several years of use.
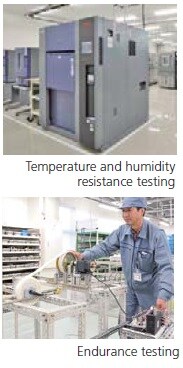
(4)Vibration Testing
Rail, truck, or other modes of transportation may be used to ship products to the customer. For example, products are tested assuming they are exposed to a variety of vibration stresses, such as being transported over a bumpy road. However, since products are normally loaded on environmentally friendly all-cardboard pallets, that is the type used for testing.
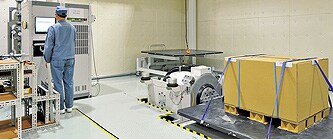
Vibration testing
Safety Assessment
(1)Safety Testing
To ensure that products can be used safely, they are tested to verify they comply with safety standards. Therefore, we even test products to determine whether or not they could cause an electric shock to customers in the event of exposure to abnormal voltages, such as lightening, for example.
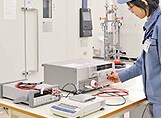
Safety testing
(2)Environmental Testing
Tests are performed to verify whether a problem that occurred in the product's electrical circuits could cause a fire or whether products designed to be waterproof will function safely when exposed to water.
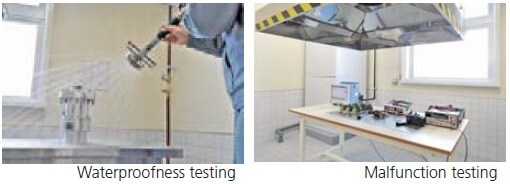
Usability Evaluation
Usability evaluation verifies that products and services are easy to use. Quality Center includes a specialized facility for usability testing. It features a separate room where monitors from within and outside the company can be observed through a one-way mirror to evaluate the safety and ease-of-use of products and services. Usability testing is performed to ensure products and services are safe, easy to use, and can be used without worry.
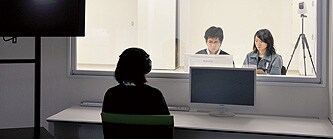
Evaluating usability
Precision Measurement and Meter Calibration
(1)Precision Measurement
Actual part dimensions and shape can be measured precisely down to 1μm (one thousandth of a millimeter) units to verify that they are as designed. Personnel with specialized expertise and qualifications test products in a room that is temperature-controlled 24 hours a day, so that only parts that pass strict inspections are used for our products.
(2)Meter Calibration
Measuring instruments or devices are the ruler used to inspect products. Therefore, in order to manufacture good-quality products based on accurate measurements, all measuring instruments and devices used within the Shimadzu Group are regularly calibrated to ensure their precision.
(3)JCSS(Japan Calibration Service System: ISO/IEC 17025 compliant)
As a calibration service provider compliant with ISO/IEC 17025 and the Japanese Measurement Act, the facility calibrates balances and weights. The JCSS calibration facility is also compliant with international mutual recognition agreements (MRA) certified by an international certification program. Therefore, certificates of calibration issued by the JCSS facility can be used in all countries that have signed the MRA.